Your cart is currently empty!
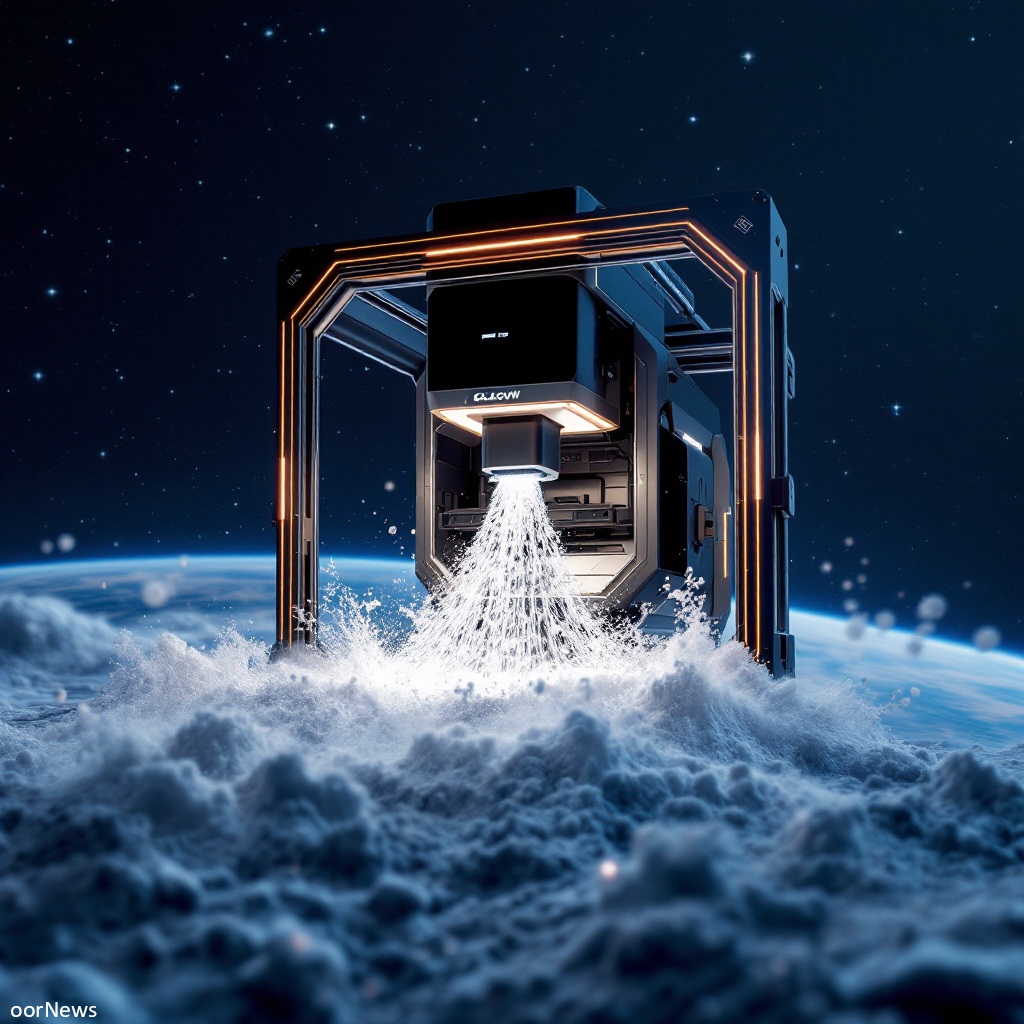
Space Manufacturing Takes Flight: Glasgow Researchers Pioneer 3D Printing in Zero Gravity
Space Manufacturing Takes Flight: Glasgow Researchers Pioneer 3D Printing in Zero Gravity
In a groundbreaking leap for space exploration, researchers from the University of Glasgow’s James Watt School of Engineering have made significant strides towards the development of orbital factories capable of 3D printing technology on demand in space. Dr. Gilles Bailet has been awarded a patent for an innovative system that tackles the challenges of 3D printing in zero-gravity environments. This technology was rigorously tested aboard the research aircraft known as the ‘vomit comet,’ which simulates microgravity conditions.
Dr. Bailet emphasizes that overcoming the hurdles of 3D printing in low-gravity could revolutionize how we manufacture equipment in orbit. This could lead to the creation of solar reflectors for zero-carbon power generation, advanced communication antennae, and even drug research stations capable of producing purer pharmaceuticals.
For years, Dr. Bailet has focused on developing a prototype 3D printer tailored for outer space. Unlike conventional printers that rely on filaments, his design utilizes a specially developed granular material that performs effectively in the vacuum of space. This unique material can be drawn from a feedstock tank and delivered to the printer’s nozzle more efficiently than traditional methods.
The research team is also investigating ways to embed electronics into the printed materials, paving the way for functional components in devices created in space. Dr. Bailet explains, “Currently, everything that goes into Earth’s orbit is built on the surface and sent into space on rockets. These rockets have strict weight limits and can damage cargo during launch. If we could establish fabricators in space, we would eliminate these constraints, allowing for more ambitious projects.”
The recent tests conducted during the 85th European Space Agency parabolic flight campaign demonstrated the prototype’s effectiveness in microgravity. The team monitored the printer’s dynamics and power consumption during 22-second weightless intervals, confirming that the system performed as designed.
Dr. Bailet is optimistic about the future, stating, “We’ve tested the technology extensively in the lab and now in microgravity. We’re confident it’s ready to produce antennae and other spacecraft parts in space.” He highlights the potential for 3D-printed space reflectors to harness solar energy continuously, contributing to net-zero goals. Furthermore, crystals grown in space could yield improved drugs, such as insulin that is nine times more effective, significantly enhancing the lives of diabetic patients.
Looking ahead, Dr. Bailet and his team are seeking funding to support the first demonstration of their technology in space. They are committed to ensuring that future manufacturing projects do not exacerbate the growing issue of space debris. This pioneering work is backed by funding from the University of Glasgow’s Glasgow Knowledge Exchange Fund and the EPSRC Impact Acceleration Account, alongside support from the UK Space Agency.
The dawn of space manufacturing is on the horizon, and with it comes the promise of a new era in technology and sustainability beyond our planet.